3 best practices for effective red zone monitoring
Red zones are the highest-risk areas on offshore drilling rigs. By using specialized red zone monitoring tools, operators can keep crew members safe during drilling, and continuously improve the safety of their operations based on their historical performance.
.webp)
Red zones are the highest-risk areas on offshore drilling rigs, where the critical drilling operations take place and where crew members are mostly likely to be in danger.
While on-site crews are essential to the drilling process, the more crew members you have, the higher the risk of serious incidents caused by remotely operated equipment and dropped objects. It also increases the risk of more minor incidents which often still require downtime.
This is because human behaviour can be unpredictable and is subject to human error, especially in extreme environments like offshore rigs.
Effectively managing red zones using specialized tools, enables offshore drilling operators to keep all crew members safe during drilling, and to continuously improve their operations based on their historical performance.
What is a red zone?
The red zone refers to the highest-risk areas where heavy machinery is moving up and down and only highly skilled crew members are permitted access. It has a static geofence and should be clearly marked at the rig with appropriate physical and digital safety signage and tools (e.g. traffic light system).
How to implement effective red zone monitoring
So how can operators manage their red zones more effectively? To help you understand how to improve red zone monitoring at your offshore drilling rigs, we’ve shared 3 best practices below.
1. Deeply understand your operations in the red zone
First you need to fully understand the red zone at your specific drilling rig, and configure your tools to ensure its geofence is reflected accurately. This includes assessing all possible risk areas at the rig and reviewing existing operational processes.
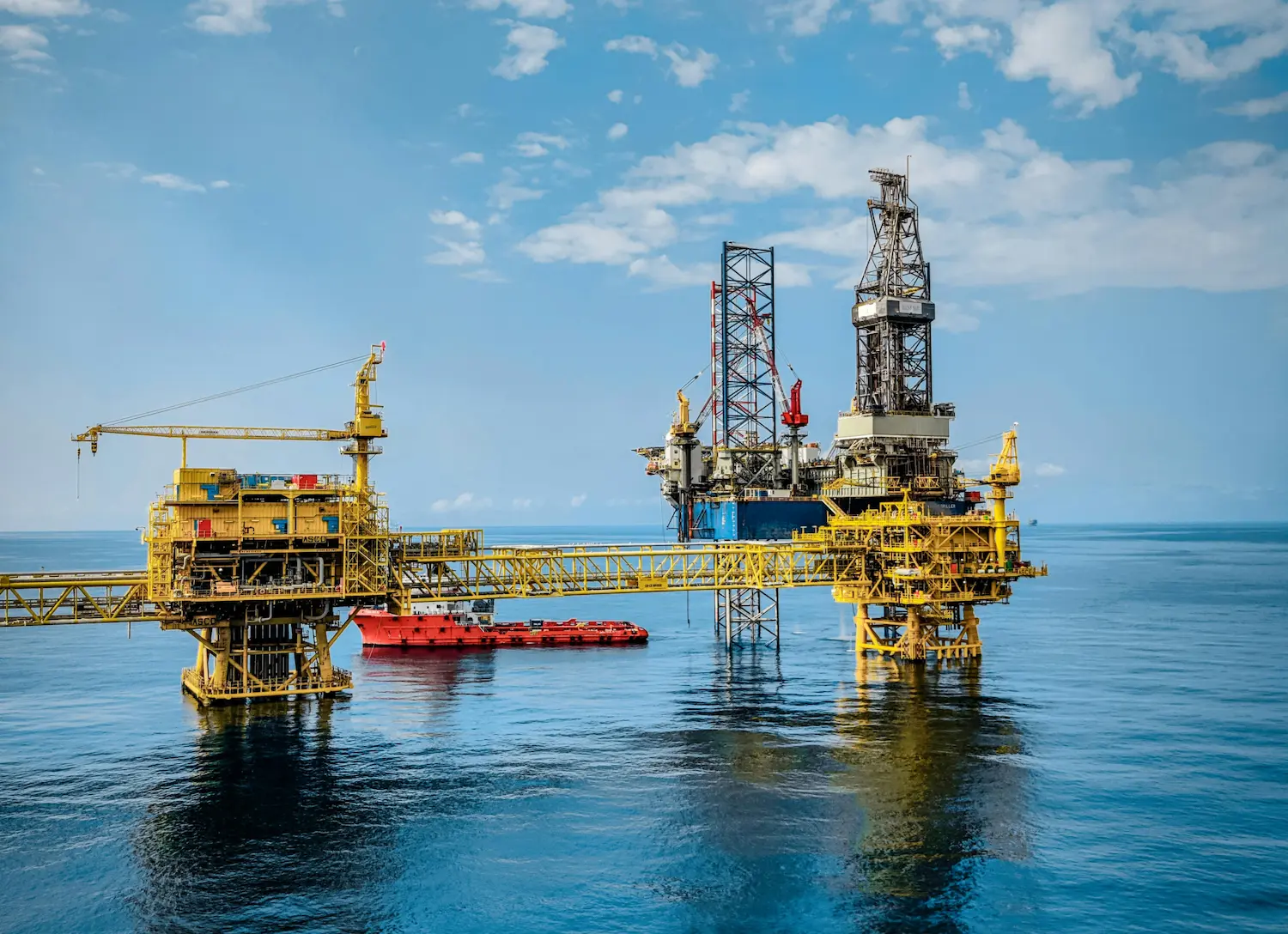
Your red zone should be regularly reviewed and updated based on actual experience, on-site changes such as moving equipment, and industry best practices.
For example, if an accident or near miss occurs in an area close to but not in the red zone, the rig operator should assess whether the red zone should be expanded to include this area going forward.
All personnel who enter the drilling rig should be trained on the exact area of the red zone and its protocols, including emergency response. Crew members who are required to enter the red zone should receive even more comprehensive training on safely operating in that area, and pass a test/certification before receiving authorization to enter the area.
Finally, the status of the red zone (whether it’s active or inactive) should be clearly visible to all personnel on-site or who are involved in the operation of the red zone.
2. Implement red zone monitoring tools
Luckily for you, specialized tools for red zone monitoring and management have emerged over the last decade, ranging from simple traffic light systems to advanced real-time visibility and alerts.
Our Red Zone Manager is designed to increase situational awareness during drilling operations, with an intuitive user interface to inform the drill crew when people enter a red zone and special status lights to alert them when they are in an unsafe area at that moment.
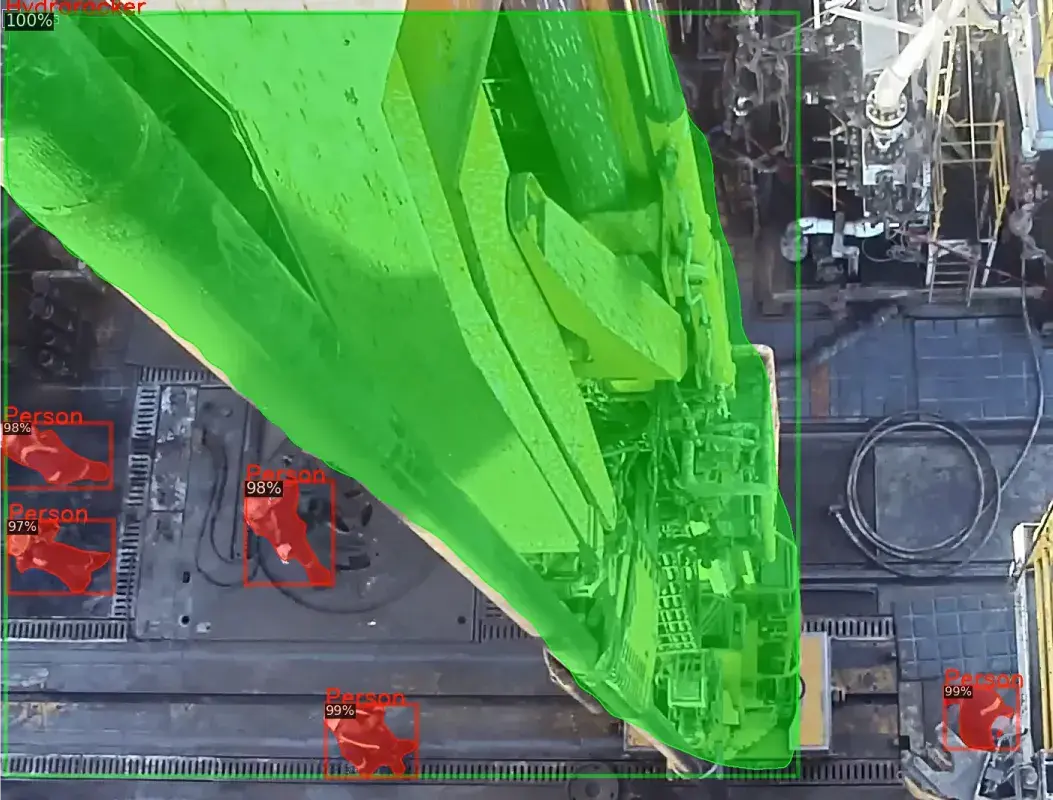
Unlike other tools, our Red Zone Manager provides real-time processing to ensure the driller is immediately alerted and can take action before or when an unsafe situation occurs. It outperforms 99% of all other analytics solutions with an end-to-end latency of only 150 milliseconds.
Red Zone Manager is designed for real-time monitoring. In a test at Noble’s offshore rig, the time between a crew member being captured by the CCTV cameras and the alarm being raised took close to 150ms. Source: Helin
Accurate people detection is at the heart of Red Zone Manager, with advanced video analytics to monitor crew members’ locations (even in so-called ‘blind spots’) but without the need for them to wear sensors or tags. It also easily integrates with existing equipment as it is hardware-agnostic.
Using red zone monitoring tools like this hugely improves the efficiency of offshore drilling, keeping crew members safe and also reducing downtime of the rig by minimizing incidents.
3. Regularly analyze insights and provide after-action reviews
While using red zone monitoring helps to significantly reduce offshore drilling incidents, it is simply not possible to prevent all accidents and near misses from occurring. This is why you need to regularly analyze the human performance and overall safety of your drilling operations.
Good red zone monitoring tools will have the capability to review the overall performance of your drilling operations (including both drilling efficiency and human safety metrics) so that you can identify and implement improvements. This should be done at least quarterly.
Additionally, after-action reviews should be conducted following any major incidents or near misses to immediately draw attention to the issue and implement actions to minimize the risky situation occurring again in the future.
Training materials should be updated to reflect new learnings, and existing crew members should also receive regular training to refresh their knowledge and inform them of any changes in protocols or processes.
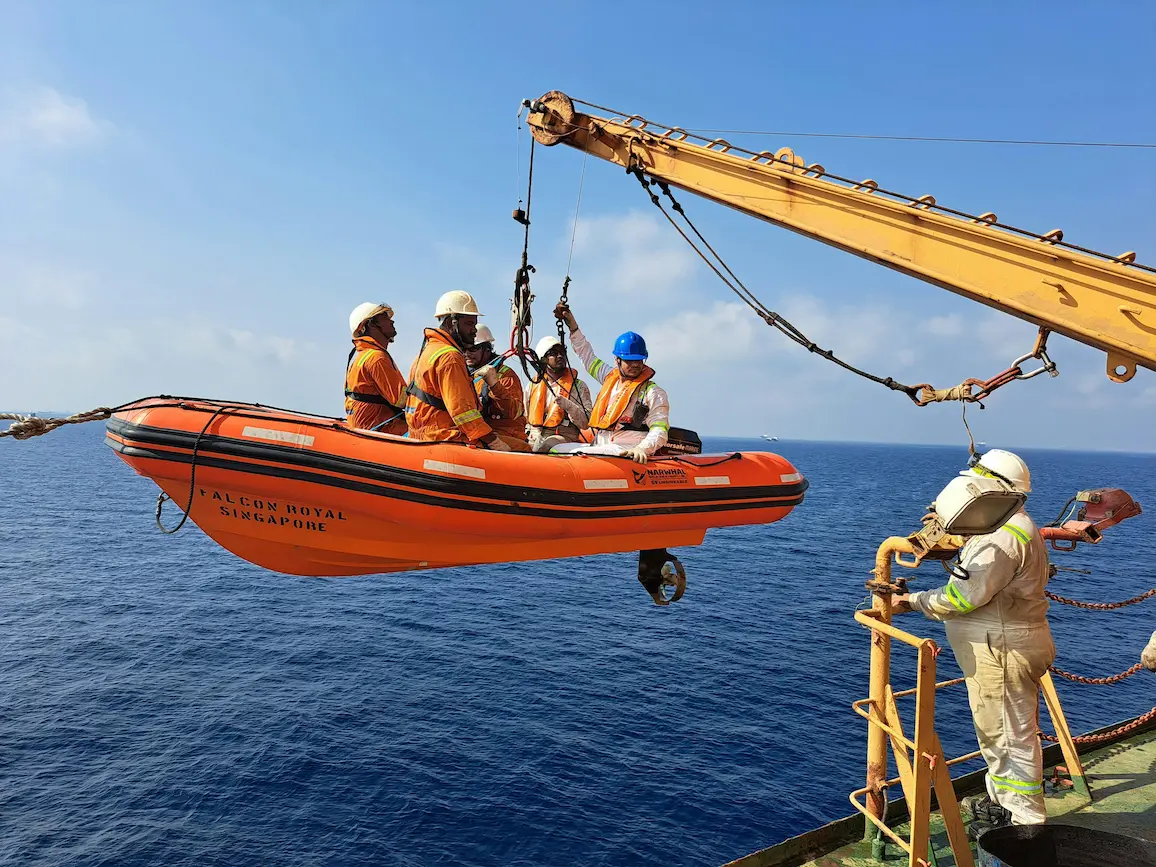
This should also include regular drills to simulate emergencies (e.g. equipment malfunction), especially for newer crew members who are less likely to have experienced the situation in real-life yet.
According to IADC’s 2023 annual report, employees with 1-5 years of service were more likely to be involved in Lost Time and Recordable injuries than employees with longer service lengths. Source: IADC ISP Program 2023
Training plays a huge role in empowering employees to identify hazards, report incidents, and act correctly in high-stress or emergency scenarios.
Bonus tip: create a continuous improvement performance cycle
To outperform on safety metrics in the offshore drilling sector, you must take a continuous improvement approach to your red zone monitoring. This involves not only reviewing past performance and implementing improvements, but also creating a feedback loop where crew members and other personnel feel that they can share their experiences and suggestions in an easy and blame-free way.
At Helin, we stay with you every step of the way on your red zone implementation journey, helping you ensure continuous improvement is built-in to how you use Red Zone Manager.
Benefits of effective red zone monitoring
Now you know how you set up your red zone monitoring effectively, but what are the benefits?
- Avoided incidents (fatalities, accidents and near misses)
- Efficient after-action reviews
- Transparent insights on actual drilling and safety performance
- Minimal equipment downtime
- In-built continuous improvement cycle
These best practices help you to provide a safer working environment for your crews and improve your performance over time.
Getting started with Helin’s Red Zone Manager
Are you ready to improve your red zone monitoring? Are you looking for a solution that easily integrates with your existing equipment and systems?
If so, you may be interested in Helin’s Red Zone Manager which provides increased situational awareness so you can improve safety for your drill crew.
Want to learn more? Make sure to get in touch for an introduction call to discuss the entire Helin platform for offshore and maritime industries, including the Red Zone Manager.
Want to read more?
Stay up to date with the latest trends and developments on the topic of industrial edge computing, monitoring and intelligence.
Get real-time insights
into your remote assets
Combine local artificial intelligence with a centrally managed data infrastructure for more accuracy, reduced congestion on your network and lower costs.

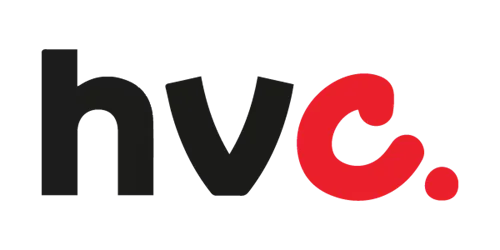
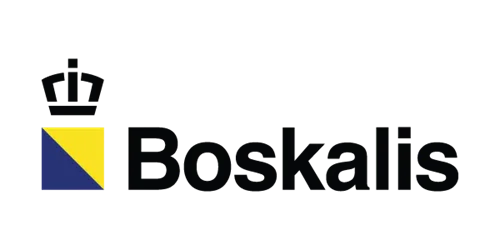