Optimized piling operations with real-time insights and remote support
Founded in the Netherlands, IQIP has provided total solutions for construction projects in the oil & gas and offshore wind sectors for over 40 years. IQIP used the Helin platform to converge data from its global fleet of piling equipment. This means IQIP could quickly analyze and resolve issues, implement preventative maintenance strategies, and increase the operational efficiency of its piling activities.
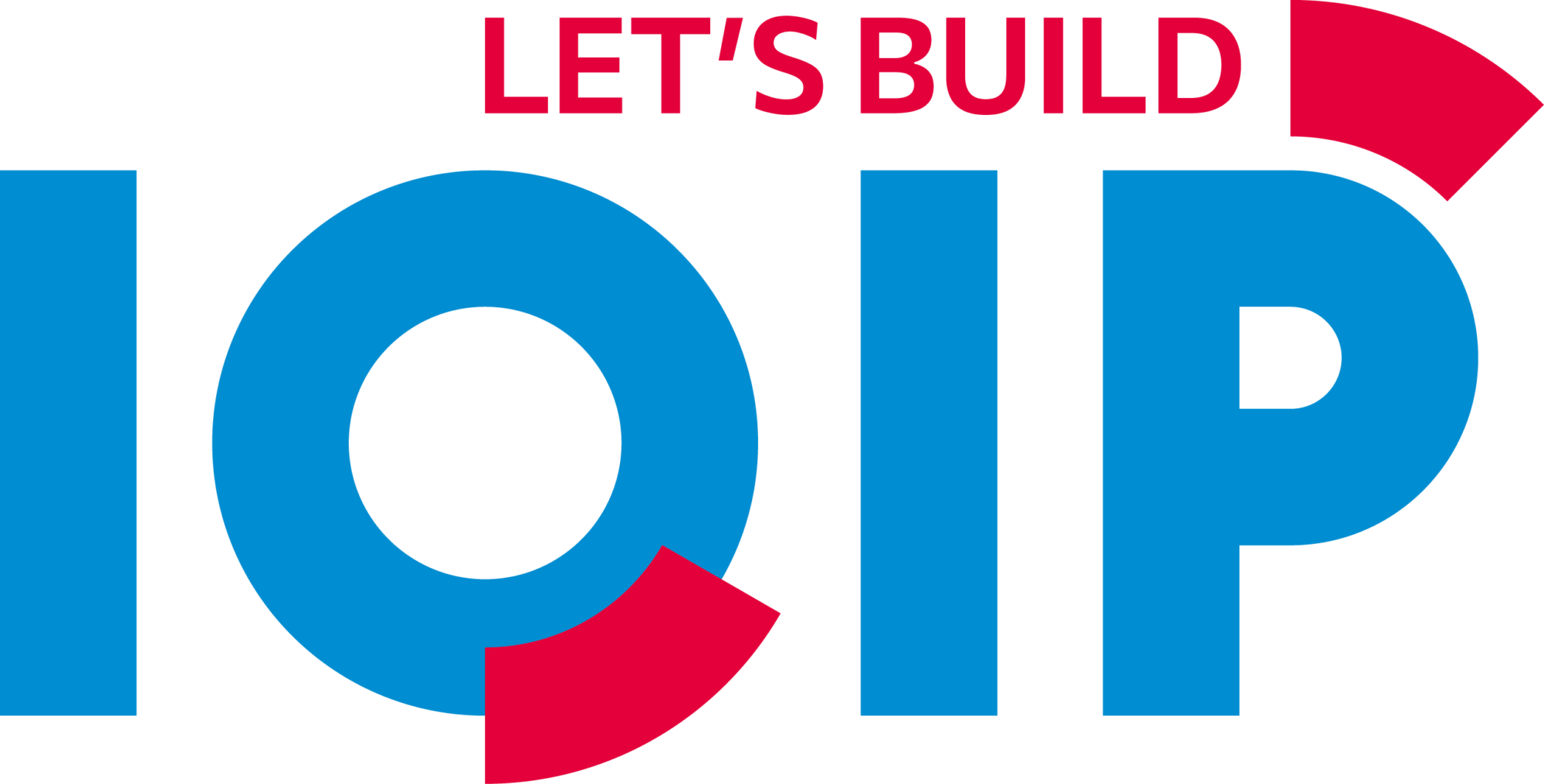
Challenge
IQIP had limited access to consolidated, real-time data from its worldwide piling operations, which could lead to unnecessary downtime and delays.
Solution
Helin implemented a scalable edge-to-cloud infrastructure that connects data from IQIP’s global fleet of piling equipment in one secure platform.
Result
IQIP uses the Helin platform for 24/7 remote support and resolution of technical issues at its sites, and for predictive maintenance strategies that avoid downtime.
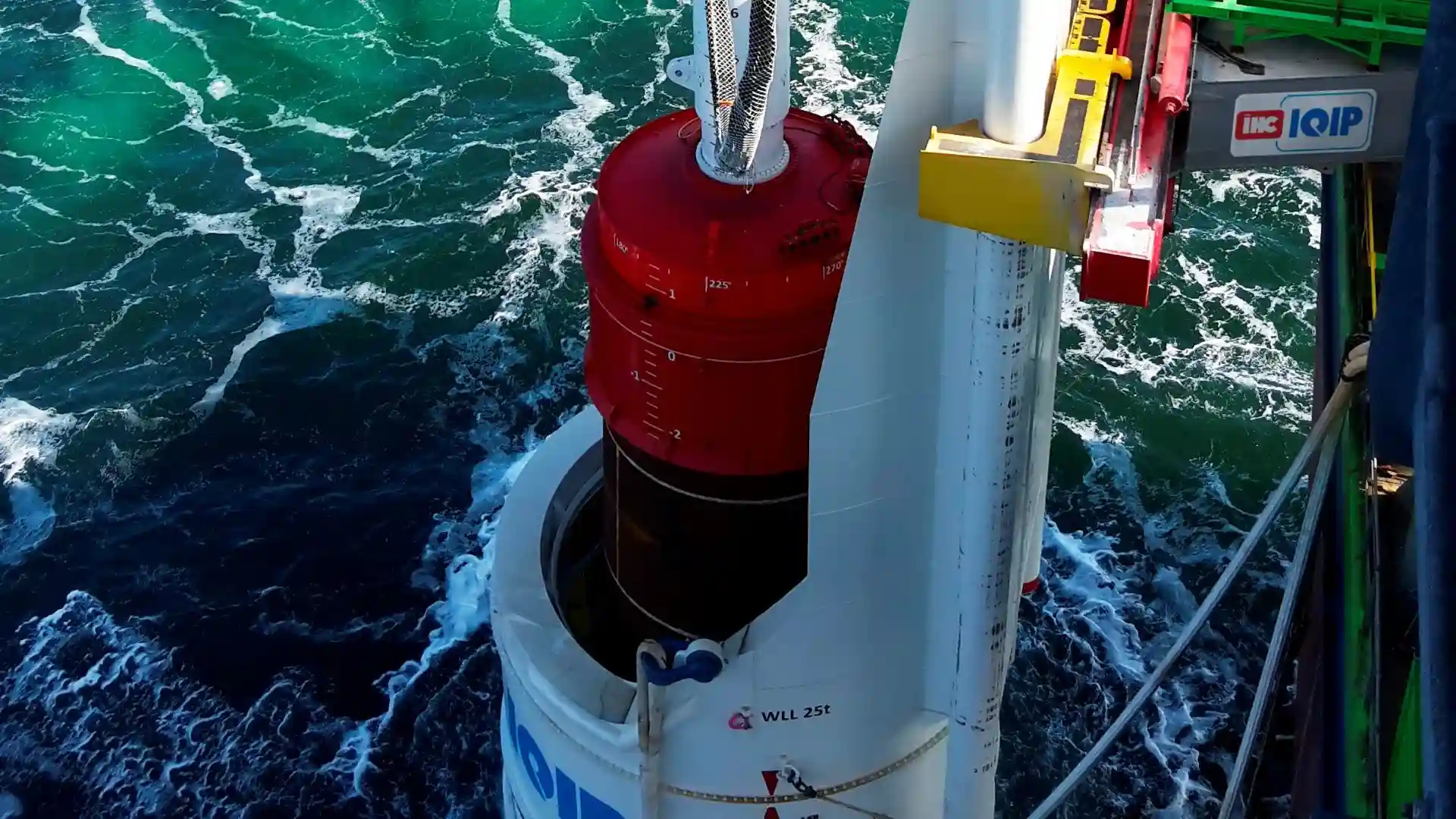
Limited visibility of piling operations meant repairs were slow and costly
As a leading OEM of piling equipment, IQIP has assets in remote locations—from Scotland to Singapore—that it needs to monitor in real-time to avoid incidents and minimize the risk of unscheduled downtime.
To do this, IQIP needs to transfer high-resolution industrial data from pumps and other rotating equipment to the cloud via 4G/LTE or SatCom. Pretty challenging when the equipment is often hundreds of kilometers offshore, piling equipment can be combined in multiple different configurations, and many industrial protocols need to be consolidated.
If this wasn’t enough, IQIP needs to be able to provide access to data, from its own equipment and equipment it rents to third parties to a range of authorized personnel, without compromising data security.
Developing a self-built solution to meet these complex needs was simply not an option as it would have eaten up huge amounts of time and money, as well as bringing edge-computing experts on board.
All of this meant that IQIP were on the lookout for an innovative technology partner who could converge data from its global fleet of equipment in a highly secure platform.
Engineering an edge-to-cloud infrastructure for IQIP’s global fleet
Enter Helin—with decades of combined experience in edge computing for offshore & maritime industries, IQIP selected Helin to develop this solution. Helin’s expert team designed and implemented a scalable edge-to-cloud infrastructure to connect data from IQIP’s global fleet of piling equipment into one secure platform.
To ensure the accurate transfer of data, Helin mounted an industrial edge node in a robust IP67 cabinet onto one of IQIP’s piling structures. This node immediately powers on when the equipment enters into operations and is built for remote offshore environments.
The node pre-processes high-resolution data, which buffers in case of connectivity loss, and allows for remote access to update and manage the configuration of the system’s settings. All the configured data is streamed into the IQIP cloud node in Microsoft Azure.
.webp)
IQIP uses the RESTful API to integrate its equipment data streams with the user portal, which makes data available for in-depth analysis by its team. New edge nodes can be added and managed from the cloud node, and off-the-shelf or custom APIs can provide additional use cases.
“Our platform has one of the quickest time to value on the market, so our customers can focus on exploring new user cases and harvesting the benefits of our platform rather than worrying about proving the ROI.” - Martijn Handels, CTO at Helin.
Next, IQIP needed to find a way to ensure that users had access to the right data streams and insights, especially for sites operated by third-party contractors.
Access to real-time operational data for authorized personnel
Luckily, the Helin platform enables easy segmentation of all data so IQIP could create custom user profiles for different datasets, equipment, and sites. This means that authorized personnel always have access to real-time, accurate data without the risk of users inadvertently gaining access to sensitive data from equipment that they’re not operating.
Combine this with the platform’s extensive authentication and cybersecurity measures, and IQIP could rest assured that its data was highly secure and protected against data breaches and cyber-attacks.
Also, by making data available remotely in one platform, IQIP avoided the risk of slowing or even postponing operations when an engineering or maintenance specialist was not available, as another specialist could easily access the same data and take over the work.
This may sound like an obvious capability, but for years many offshore and maritime companies have been over-relying on individuals with extensive experience and know-how, only to be left exposed if that person was unexpectedly sick or left the company.
With IQIP’s data connected and accessible to authorized personnel, IQIP could now focus on using this data to overhaul how their technical support handled issues.
24/7 efficient resolution of technical issues at remote sites
When operating heavy complex equipment it’s inevitable that there’ll be technical issues. Such issues need to be quickly investigated and resolved to avoid unnecessary downtime and to prevent accidents happening to crew members.
But, providing on-site support is costly, time-consuming, and logistically difficult to move specialized crews between remote locations. Imagine maintaining equipment on a site off the UK coast and then being relocated to Qatar the next day for an emergency repair.
With Helin’s platform, IQIP’s technical support teams can now conduct an intensive root cause analysis on unexpected systems failures and figure out the solution all from the comfort of their own home or office. They can even guide local support crews in implementing physical repairs if the issue can’t be solved by remote reconfigurations.

Plus, with everything investigated and resolved remotely, there’s a digital record of how the issue was handled, which can be used to learn from or improve procedures going forward.
This all leads to faster and better resolutions of issues, less logistical headaches for rota planners, less downtime, and even avoided emissions due to reduced need for flights.
Predictive maintenance reduces unplanned downtime
Another way to reduce downtime is by using condition-based maintenance and predictive maintenance. Condition-based maintenance involves monitoring the real-time condition of your industrial assets (using the right sensor data) and implementing the right maintenance cycle for your equipment based on its actual condition.
Predictive maintenance takes condition-based maintenance a step further by analyzing data to detect issues in real-time and predict potential issues before they happen. The equipment owner can then take action to resolve or prevent the issues from occurring.
The Helin platform is continuously analyzing IQIP’s equipment data so that IQIP can optimize the equipment’s performance and lifespan, without overspending or underspending on maintenance.
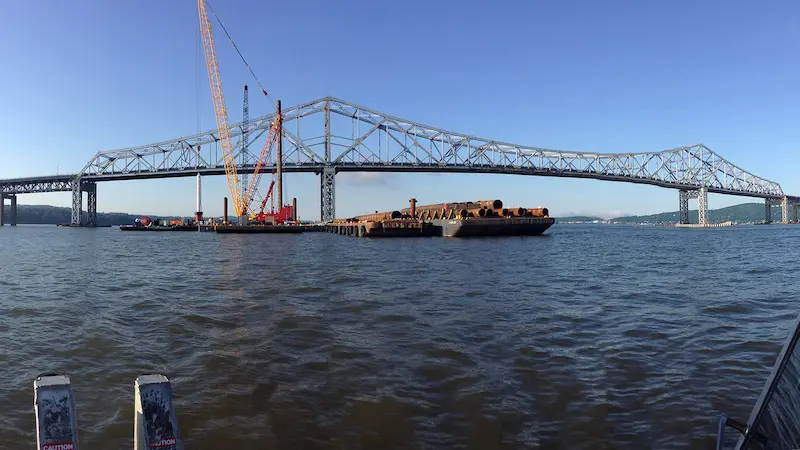
For example, piling equipment may have less wear and tear due to less usage, and thus the maintenance cycle can be safely pushed out. On the flip side, some equipment may become damaged by the ocean or another vessel (which is not always visually noticeable) and need urgent maintenance.
In either case, IQIP could use insights from the Helin platform to ensure the equipment remains safely in operation and avoid unnecessary downtime and delays. It even provides proactive enhancements, thanks to the predictive insights that the data offers.
Scalable solution with the ability to expand use cases over time
The Helin edge-to-cloud infrastructure is designed for easy and hassle-free scalability across global fleets of equipment. This includes the ability to add new nodes and custom or off-the-shelf APIs, such as the RESTful API, which integrates equipment data with user interfaces and other third-party systems.
“At Helin, we’re passionate about unlocking the full potential of industrial assets for companies in the offshore, maritime, and energy industries. We collaborate with large global OEMs like IQIP to help them take full control of their equipment’s performance with real-time monitoring, analysis, and predictive insights.” - Martijn Handels, CTO at Helin.
IQIP used the platform to enhance visibility of its remote piling operations, resolve technical issues more efficiently, and use predictive maintenance strategies to avoid unnecessary downtime.
Getting started with Helin’s platform
Are you looking to integrate your data and applications into one secure platform? Do you need to access data at remote off- and onshore sites? Our edge computing platform may be just the solution you need.
Want to learn more? Make sure to book an introduction call to discuss how Helin’s platform could work for your offshore or maritime business.
Other interesting case studies
Get real-time insights
into your remote assets
Combine local artificial intelligence with a centrally managed data infrastructure for more accuracy, reduced congestion on your network and lower costs.

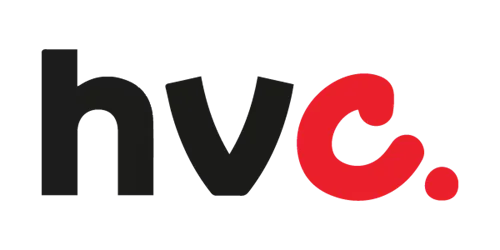
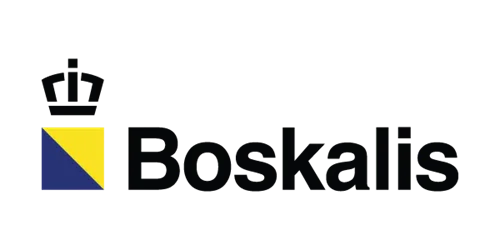