Demystifying the digital landscape: A deep dive into the top 5 industrial protocols
Industrial protocols are the frameworks that determine how operational data is stored, transferred, and protected. With a myriad of options available, how can one confidently navigate this intricate domain?
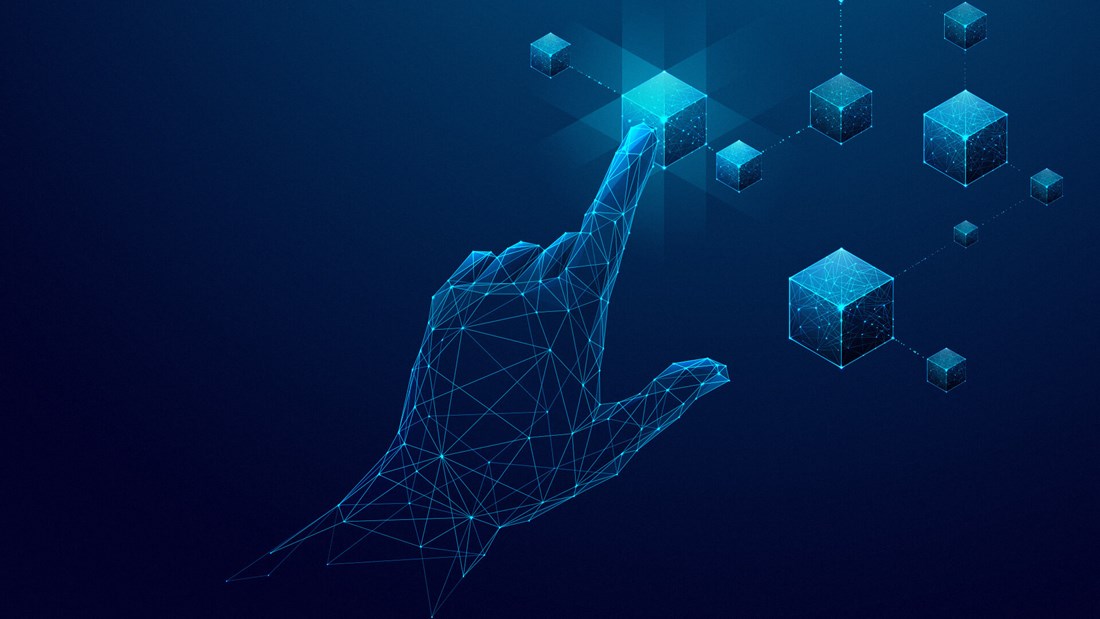
In today's interconnected industrial world, the choice of the right protocol isn't just important—it's essential. Protocols are the frameworks that determine how operational data is stored, transferred, and protected. With a myriad of options available, how can one confidently navigate this intricate domain?
The role of industrial protocols
At their core, protocols exist to ensure seamless communication between machines and systems. They are the hidden engines that facilitate the smooth functioning of our interconnected digital landscapes, bringing about efficiency, safety, and optimization.
Zooming in on the top 5 protocols
1. OPC (Object Linking and Embedding for Process Control)
OPC was originally designed for industrial automation. Its main versions are:
- OPC DA (Data Access): A prevalent choice for real-time data exchange in industrial automation. Based on Microsoft's OLE, COM, and DCOM technologies, it offers simplicity, though with some architectural limitations.
- OPC UA (Unified Architecture): A more versatile successor to OPC DA, it’s scalable, supports various platforms, and boasts strong security features. However, its richness also brings complexity, sometimes causing interoperability challenges.
2. Modbus
Modbus is a staple in manufacturing and the power industry. Modbus has two main versions:
- Modbus RTU: Primarily uses binary coding, prioritizing efficient transmission and reduced errors.
- Modbus TCP/IP: An extension allowing Modbus to function within existing Ethernet networks.
3. CAN bus (Controller Area Network)
CAN bus was initially designed for automotive systems, it's a message-based protocol. Devices in a CAN network, from microcontrollers to gateways, broadcast data across all nodes, using message prioritization.
4. Profibus
Profibus is a comprehensive suite of protocols, and its devices connect to a central line, enabling efficient data transfer and advanced diagnostic capabilities. With its roots in a German collaboration, it remains a top pick in industrial automation.
5. The analog vs. digital debate
Analog protocols, such as CAN bus and Profibus, offer unique advantages in signal sampling but can face transmission challenges. In contrast, digital protocols like OPC provide enhanced data accuracy and reliability, especially over long distances.
Key Considerations
Before diving headfirst into a protocol choice, here are pivotal questions to ponder:
- Analog or digital: Which aligns with your operational needs?
- Scalability: Will it grow with your enterprise?
- Security: How robust are its protective measures?
- Data Exchange Control: How is the exchange steered and controlled?
- Interoperability: Can different components communicate seamlessly?
Selecting the right industrial protocol
Selecting the right protocol extends beyond understanding its technicalities; it’s about ensuring it aligns seamlessly with your organization’s operational needs. Always consider consulting with specialists or machinery suppliers to ensure an optimal match.
The Helin Platform, our SaaS Industrial Edge Intelligence solution, is equipped to adeptly manage edge devices across a wide range of industrial assets and all of the above protocols and many more.
By harnessing the power of these protocols, we stand at the forefront of the energy transition, heralding an era of unparalleled efficiency, safety, and sustainability.
Want to read more?
Find all the latest news and relevant knowledge on topics like smart buildings, building data, and modern healthy workspaces.
Get real-time insights
into your remote assets
Combine local artificial intelligence with a centrally managed data infrastructure for more accuracy, reduced congestion on your network and lower costs.

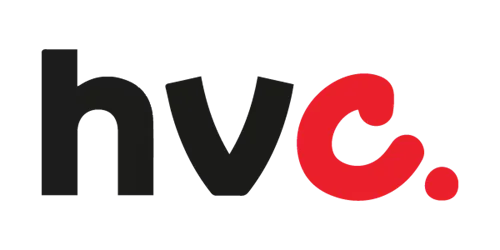
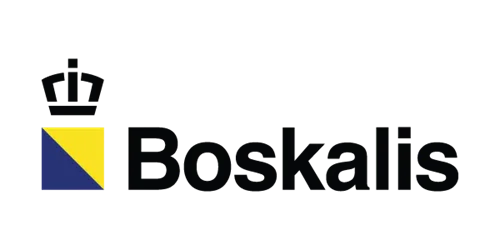